Case Study: How Abcur Equipment Inc Helped a Local Business Boost Efficiency
Introduction
In today's fast-paced business environment, efficiency is key to staying competitive. Local businesses often struggle to keep up with larger corporations due to limited resources. However, with the right support and tools, they can significantly enhance their operations. This case study explores how Abcur Equipment Inc helped a local business boost its efficiency and productivity.
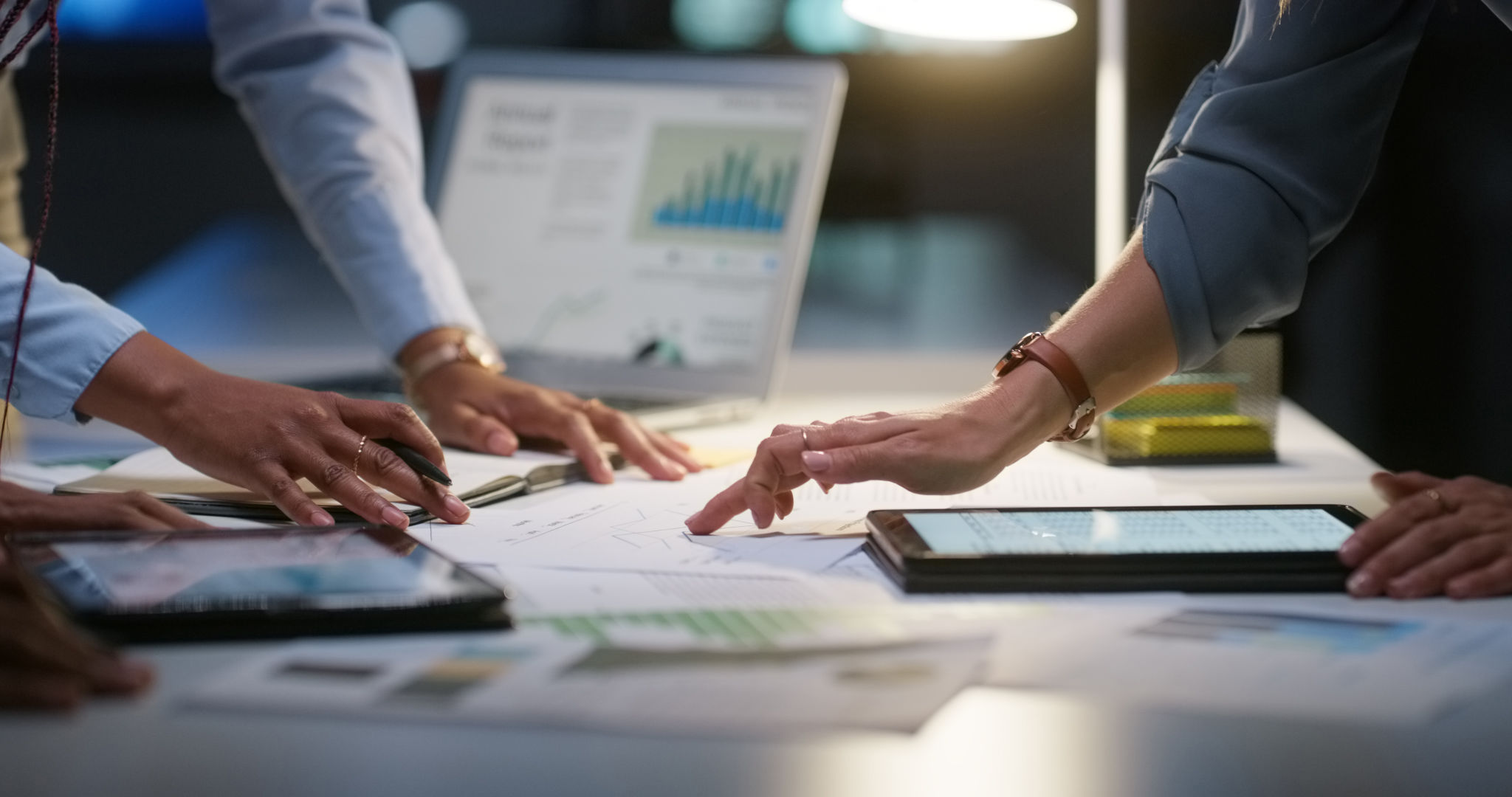
Understanding the Challenge
The local business in question, a mid-sized manufacturing company, was facing several operational challenges. The main issues included outdated equipment, high maintenance costs, and inefficient workflows. These problems were causing delays in production and impacting overall profitability.
Recognizing the need for a solution, the business decided to partner with Abcur Equipment Inc, a leading provider of industrial equipment and solutions. Their goal was to modernize their operations and improve their bottom line.
The Solution Provided by Abcur Equipment Inc
Abcur Equipment Inc conducted a thorough assessment of the manufacturing company's needs. Based on their findings, they developed a tailored plan to address the specific challenges faced by the business. The solution included:
- Upgrading existing machinery with state-of-the-art equipment.
- Implementing automated systems to streamline production processes.
- Providing comprehensive training for employees on new technologies.
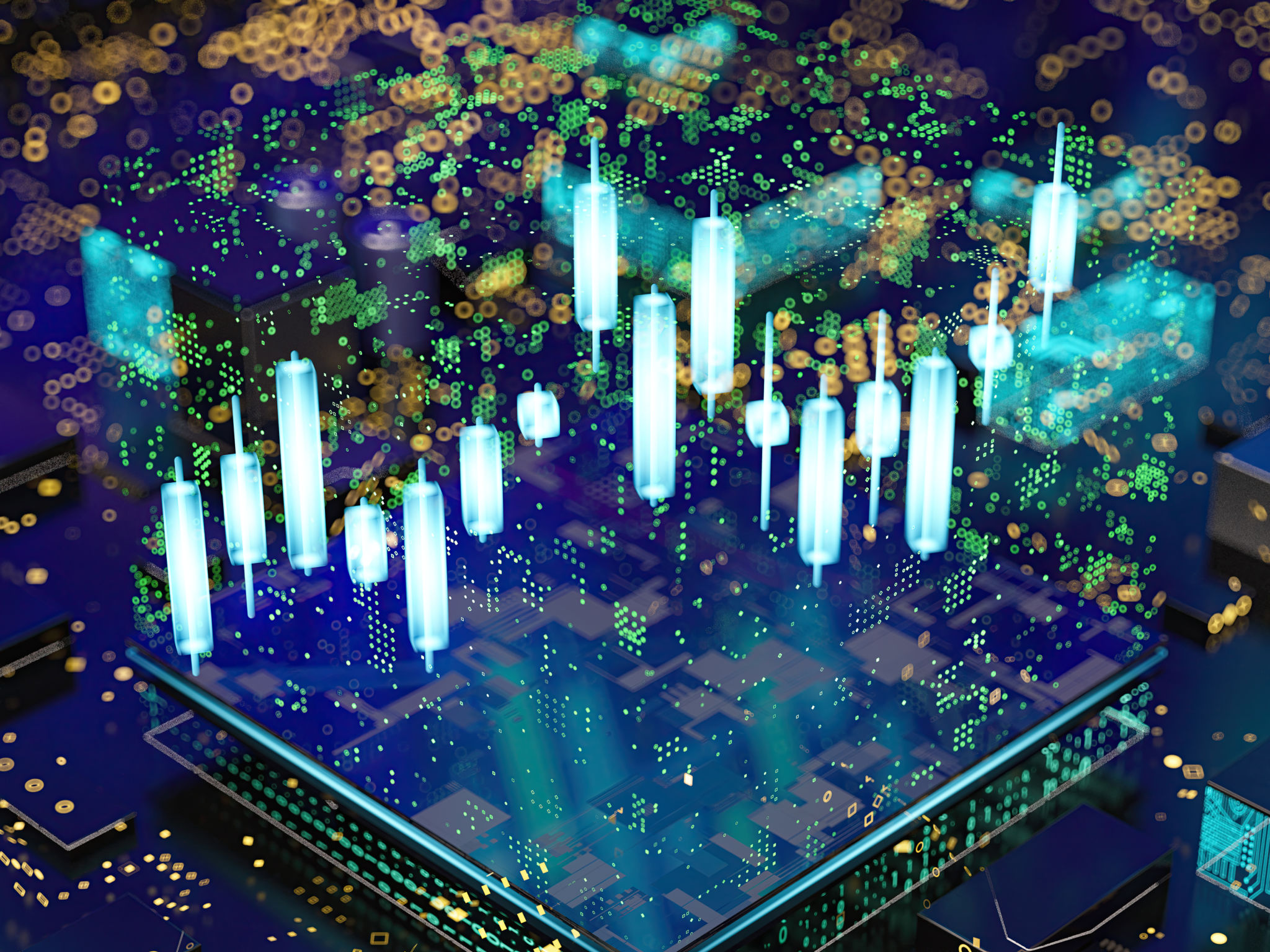
Implementation and Results
The implementation process was smooth and efficient, thanks to the expertise of Abcur Equipment Inc's team. They worked closely with the manufacturing company's staff to ensure minimal disruption during the transition. The new equipment and systems were successfully integrated into daily operations.
As a result, the business experienced a significant boost in efficiency. Production times were reduced by 30%, maintenance costs decreased by 20%, and overall output increased by 25%. These improvements translated into higher profits and a stronger market position.
Employee Feedback and Engagement
One of the key factors contributing to the success of this project was employee engagement. Abcur Equipment Inc provided hands-on training and support, ensuring that staff felt comfortable with the new technologies. Employees appreciated the investment in their professional development and were motivated to adapt to the changes.
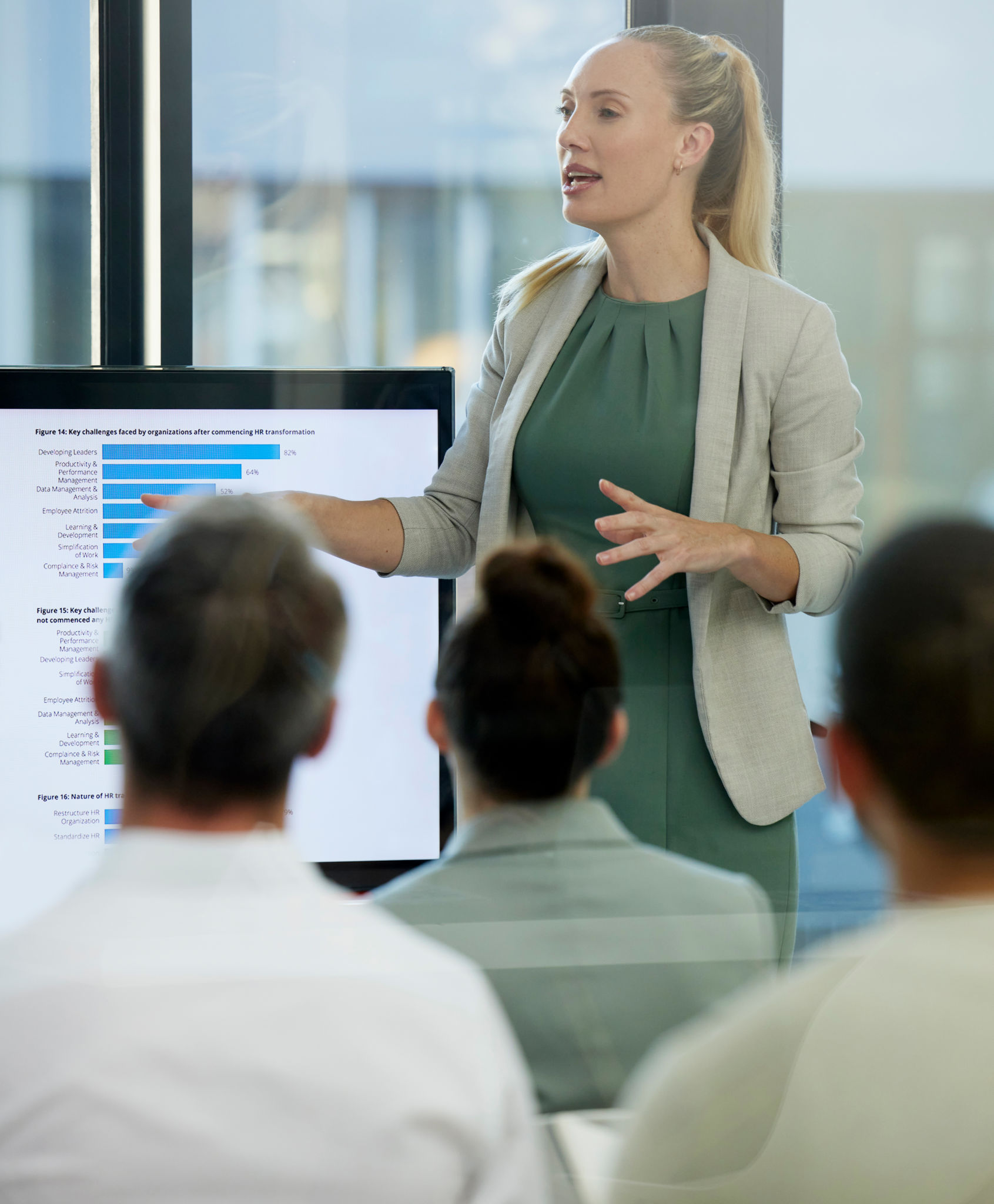
Conclusion
The partnership between the local manufacturing company and Abcur Equipment Inc serves as a prime example of how targeted solutions can transform business operations. By investing in modern equipment and technologies, businesses can enhance their efficiency and competitiveness in the market.
For other local businesses facing similar challenges, this case study demonstrates the potential benefits of collaborating with industry experts like Abcur Equipment Inc. Embracing innovation and upgrading outdated systems can lead to significant improvements in productivity and profitability.